Tank Bottoms Inspection: MFL/STARS VS SLOFEC
By: Eng. Jesus Eduardo Contreras
The probability of failure in a storage tank can be low but the consequences can be catastrophic. A leaking storage tank can not only cause serious environmental problems, affect human and animal life around it, but can also have a major impact on the profitability of the operation in the form of product loss, unscheduled downtime and prolonged repairs to rectify the damage, as well as environmental remediation and non-compliance with legislative clauses.
That is why the inspection of them and especially the bottom plays an important factor. Full surface coverage with NDT inspection was often prohibited due to inappropriate methods that are time-consuming and therefore too expensive. This created the demand for so-called detection tools with which suspicious areas can be detected very quickly. In recent years, several of these methods have been introduced to the market. This article will discuss two methods that can be applied to carbon steel components.
The first method is based on Magnetic Flux Leakage (MFL) and is suitable for the inspection of magnetic components. And the second is SLOFEC or Saturated Low Frequency Eddy Current, for both kind of materials: Magnetics and Non-magnetics, now the question is not really which is better, but which may be most appropriate for a given inspection. And that is what we will try to answer here!
Let see the operational principles for each method!
MFL/STARS Principles
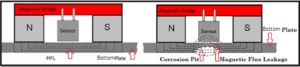
The scanner magnet creates a localized magnetic field that “saturates” the full thickness of the plate. The material loss (corrosion) causes the magnetic field to “leak” out of the plate and this leakage field is detected by MFL sensors (Hall effect and STARTS) and the resulting signals are processed to estimate percentage loss and the discrimination top/bottom defects.
SLOFEC Principles
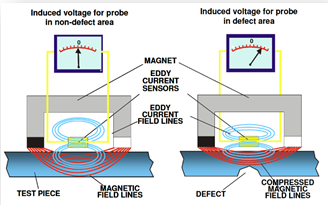
The SLOFEC inspection technique uses the eddy current principle in combination with a magnetic field. Utilizing superimposed DC-magnetization, the depth of penetration of the eddy current field lines in the ferromagnetic material is increased.
In case of a defect, the magnetic field lines have a higher density in the remaining wall thickness, which consequently changes the relative permeability in the area, which again changes the eddy current field lines, as shown in Diagram.
The changes of the eddy current field lines are measured and analyzed in comparison to its calibration in difference of the signal amplitude and the signal phase.
Let see some characteristics for each method!
Magnetic Flux Leakage (MFL)(w/STARS) | Saturated Low Frequency Eddy Current (SLOFEC) |
The MFL method can only be applied on low alloy carbon steels which have a high magnetic permeability. Now some manufacturers are developed STARS sensors (Surface Topology Air Gap Reluctance Sensor), working together with MFL sensors (Hall effect) that determines whether corrosion is top side or bottom side. STARS also provide a simple visual representation of the inspection surface through thick non-magnetic material up to 10 mm (0.39 po) thick. MFL Bottom Scanners are some of the fastest motor-driven scanners on the market. It is capable of variable speeds up to 1 m/s (3.2 ft/s). The high-resolution sensors give an excellent Probability of Detection (PoD) of a defect as small as 2 mm (0.08 in) in diameter in 10% Estimate Percentage of Loss (EPL). Now with the most recent development, new scanner reaches out an optimum in performance compare with traditional MFL tools. Consequently, tanks bottom thickness range is increasing to 15 or at best 18+ mm under favorable circumstances. Average Weight equipment: 60 kg. Very often this mainly qualitative character is acceptable for industry in return for its high speed, full surface coverage and in particular its high probability of defect detection. |
Capability of inspecting ferromagnetic and non-ferromagnetic materials such as carbon steel, stainless steel, duplex, and super duplex materials. Speed average 0.4m/s. |
Learn more about NDE for STORAGE TANKS inspection here! More details about MFL techniques, don’t hesitate to contact with us!